A Comprehensive Overview to the Refine and Advantages of Plastic Extrusion
In the vast realm of production, plastic extrusion arises as a extremely reliable and crucial procedure. Transmuting raw plastic into continual accounts, it satisfies a huge selection of industries with its remarkable convenience. This guide intends to elucidate the complex steps included in this method, the kinds of plastic suitable for extrusion, and the game-changing advantages it brings to the market. The following discussion assures to unravel the real-world impacts of this transformative procedure.
Comprehending the Essentials of Plastic Extrusion
While it may appear complicated at very first glance, the process of plastic extrusion is fundamentally simple. The procedure starts with the feeding of plastic product, in the kind of granules, pellets, or powders, right into a heated barrel. The shaped plastic is then cooled, solidified, and cut right into preferred lengths, completing the procedure.
The Technical Refine of Plastic Extrusion Explained

Sorts Of Plastic Suitable for Extrusion
The choice of the appropriate type of plastic is a critical element of the extrusion procedure. Numerous plastics provide special properties, making them more fit to particular applications. Recognizing these plastic kinds can dramatically enhance the extrusion process.
Comparing Plastic Extrusion to Various Other Plastic Forming Approaches
Recognizing the kinds of plastic suitable for extrusion leads the method for a wider discussion on how plastic extrusion compares to various other plastic developing techniques. These consist of shot molding, strike molding, and thermoforming. Each approach has its distinct uses and advantages. Injection molding, for instance, is outstanding for creating elaborate components, while impact molding is best for hollow items like bottles. Thermoforming excels at forming superficial or big parts. Plastic extrusion is unequaled when it comes to developing continuous accounts, such as gaskets, seals, and pipelines. It likewise enables a consistent cross-section along the size of the product. Hence, the option of technique mostly relies on the end-product demands and specifications.
Secret Benefits of Plastic Extrusion in Manufacturing
In the world of manufacturing, plastic extrusion offers many substantial advantages. One noteworthy advantage is the cost-effectiveness of the procedure, that makes it an economically appealing production approach. In addition, this strategy provides superior product adaptability and improved production rate, thereby enhancing total production efficiency.
Economical Manufacturing Approach
Plastic extrusion jumps to the center as a cost-effective production technique in production. Furthermore, plastic extrusion calls for much less energy than typical manufacturing techniques, adding to reduced functional expenses. Overall, the monetary benefits make plastic extrusion an extremely appealing choice in the manufacturing market.
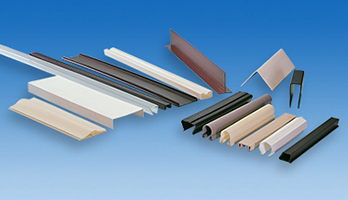
Superior Product Flexibility
Beyond the cost-effectiveness of plastic extrusion, another considerable benefit in making lies in its exceptional item adaptability. This makes plastic extrusion a perfect remedy for sectors that require personalized plastic components, such as auto, building and construction, and product packaging. In essence, plastic extrusion's item flexibility fosters development while improving functional performance.
Enhanced Manufacturing Speed
A significant benefit of plastic extrusion lies in its improved manufacturing rate. Few various other production procedures can match the speed of plastic extrusion. Furthermore, the ability to preserve consistent high-speed manufacturing without sacrificing product quality establishes plastic extrusion apart from various other techniques.
Real-world Applications and Influences of Plastic Extrusion
In the realm you can try here of production, you could try these out the method of plastic extrusion holds extensive relevance. The economic benefit of plastic extrusion, mostly its affordable and high-volume outcome, has revolutionized manufacturing. The industry is persistently making every effort for advancements in recyclable and eco-friendly products, indicating a future where the advantages of plastic extrusion can be preserved without jeopardizing ecological sustainability.
Final thought
Finally, plastic extrusion is a very effective and reliable approach of transforming raw materials into varied items. It uses countless advantages over other plastic developing methods, including cost-effectiveness, high outcome, minimal waste, and style adaptability. Its impact is exceptionally really felt in various markets such as building and construction, vehicle, and customer items, making it a pivotal process in today's production landscape.
Diving much deeper right into the technical process of plastic extrusion, it begins with the choice of the proper plastic product. Once cooled, the plastic is cut into the needed lengths or wound onto reels if the product is a plastic wikipedia reference film or sheet - plastic extrusion. Contrasting Plastic Extrusion to Various Other Plastic Forming Approaches
Understanding the types of plastic appropriate for extrusion paves the method for a more comprehensive conversation on just how plastic extrusion stacks up against other plastic developing methods. Couple of other manufacturing processes can match the speed of plastic extrusion.